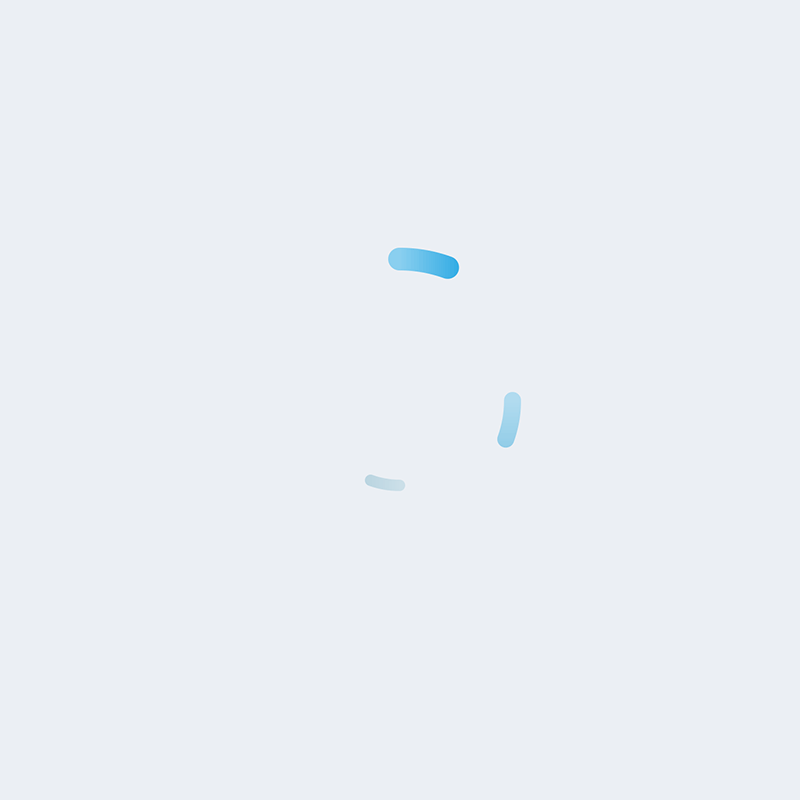
3D scanning
3D scanning technology
3D digitization (scanning) takes place using a measuring arm with a digitizing laser head. If necessary, the digitizing laser head can be replaced by touch probes (balls) and the arm can serve as a hand-held CMM measuring device.
3D digitization (3D scanning) is used to digitize real shapes in order to obtain 3D computer geometry. This can then be used either as a default source of 3D geometry for Reverse Engineering or in the inspection area to compare parts with CAD models.
Technical specifications
- Scanning technology: laser
- Accuracy: +/- 0.05 mm
- Arm range: 2.5 m
- 3D data output format: *.stl
Materials
- Evaluation of dimensions
- Evaluation of shape and position tolerances
- Area comparison of the source with a CAD model
- Control sections – curves (possibility of export to IGES)
- Setting the source to CAD according to the customer's request (RPS points, Best-FIT, setting 3-2-1)
- Measurement protocols in 2D (pdf, html)
- Measurement protocols in 3D (3D viewer free to download)
Advantages of 3D scanning
How it works
Shape capture
A 3D scanner (e.g. laser or structured light) is used to capture the shape of a physical object. Scanning is done from multiple angles to get the complete geometry.
Step 2
The result is a so-called point cloud - millions of coordinates that describe the surface of an object. This is then converted into a triangular mesh, e.g. in STL format.
Adjustment and alignment
The model is cleaned of noise or aligned to the correct position. It can then be used for measurements, quality control or as a basis for further processing.